Crushing Machines
Jaw Crusher
Jaw crushers are widely favored as primary crushers for coal in mining and quarrying operations where significant coal volumes are extracted. These crushers operate on the principle of compressing coal between a fixed jaw and a movable jaw for coarse crushing. The jaws are lined with hard materials like manganese steel to facilitate efficient coal crushing.
- Capacity: 1-2,200 t/h
- Feed size: ≤1,200 mm
- Output size: 10-350 mm
- Advantages: Robust and durable construction, high crushing ratio, accommodating large feed sizes, uniform particle size distribution, minimal fine powder generation, simple structure
- Disadvantages: Requires frequent maintenance for jaw plate wear, less efficient with sticky materials, potential for dust pollution
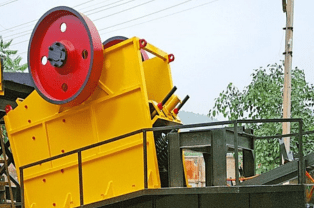
Gyratory Crusher
Gyratory crushers, although uncommon in coal processing, find utility in primary crushing of large dry or slightly wet coal. Featuring larger feed openings compared to jaw crushers, they offer higher output.
A gyratory crusher functions by compressing coal between a mantle and a fixed concave liner, similar to a cone crusher.
- Production output: 2,354-14,082 t/h
- Feed size: 1,350 mm
- Advantages: High output and continuous operation, accommodates unlimited feed size, high crushing ratio, fine discharge particle size, minimal dust pollution
- Disadvantages: High initial investment, complex structure leading to high maintenance costs, unsuitability for moist materials
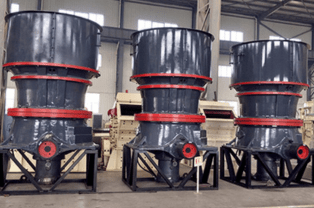
Double Toothed Roll Crusher
Double toothed roll crushers represent economical and practical solutions for medium and fine coal crushing, particularly favored in small coal processing plants.
These crushers suit medium-hard coal with high moisture content (exceeding 25%), such as raw coal, coke, lignite, and activated carbon.
A double toothed roll crusher comprises two parallel toothed rollers rotating in opposite directions, crushing coal between them to produce uniform particles.
- Capacity: 3-110 t/h
- Feed size: ≤30 mm
- Output size: 2-10 mm
- Advantages: Versatile material adaptability, minimal risk of blocking, low over-grinding rate, uniform cubic particle output, low maintenance, low energy consumption
- Disadvantages: Lower output compared to other crushers, noisy operation, requires frequent maintenance
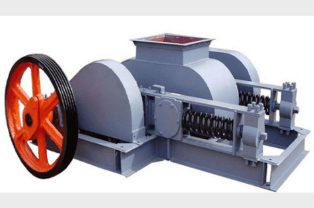
Impact Crusher
Impact crushers excel in secondary and tertiary coal crushing, especially for high-moisture content coal. Positioned after jaw crushers, they experience minimal blockages or motor issues.
Comprising a rotor with hammers or blow bars, impact crushers utilize the high-speed rotor’s impact force for medium and fine coal crushing.
- Capacity: 1-2,000 t/h
- Feed size: ≤800 mm
- Output size: 2-80 mm
- Advantages: Exceptionally high crushing efficiency, uniform discharge particle size, easy maintenance, low energy consumption
- Disadvantages: Vulnerable to wear due to high-speed impacts, potential for noise and dust pollution
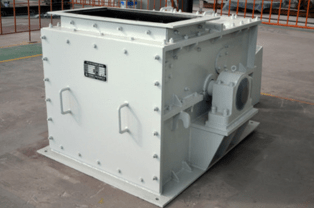
Hammer Crusher
Hammer mills are preferred in most coal plants for handling medium to bituminous coals of varying hardness. A single hammer mill crusher can efficiently break coal into desired sizes, integrating coarse and medium crushing stages, thus saving processing time and costs.
Operating on the principle of rotating hammers, hammer crushers crush material into finepowders.
- Capacity: 1-3,000 t/h
- Feed size: ≤1,000 mm
- Output size: 5-35 mm
- Advantages: Streamlined crushing process, high crushing ratio, uniform output size, reduced over-crushing, simple structure, easy operation and maintenance, cost-effectiveness
- Disadvantages: Inadequate for highly moist coal (exceeding 10%), prone to clogging, may produce coarse discharge particles, potential for dust pollution.
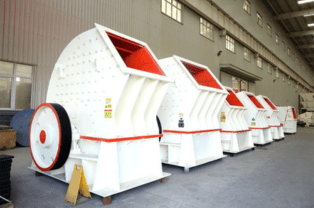