Rotary Dryer Machine
What is Rotary Dryer Machine ?
The rotary dryer machine, also referred to as a rotary drum dryer, is an industrial drying apparatus capable of drying high-humidity materials through direct or indirect heating. Consisting of a tilted or horizontally oriented rotating cylinder, the rotary drum dryer holds a pivotal position in chemical, agricultural, coal, building materials, and light industrial sectors. It is favoured for its substantial processing capacity, sturdy construction, and adaptability to diverse raw materials. Whether drying fertilizer for optimal granulation, sand for enhanced quality, limestone for improved grinding efficiency, or regulating the moisture content of biomass for easier briquetting, the rotary dryer proves indispensable. Notable for its wide supply range and straightforward operation, it requires materials to be dried to a water content of 3-10% to meet briquetting requirements.
Advantages of Rotary Dryer
- Cost Efficiency: Rotary dryers offer low operating costs, primarily due to their energy efficiency, requiring minimal maintenance. This results in reduced operational expenses, particularly beneficial for potash ore drying.
- High Capacity: With the capability to handle substantial ore volumes, rotary dryers are well-suited for large-scale operations. Their capacity can reach up to 30 metric tons of ore per hour, surpassing other drying methods.
- Customizable Design: Rotary dryers can be tailored to meet the specific requirements of potash ore processing plants. Their design flexibility allows adjustment for various ore sizes and moisture levels, accommodating diverse applications.
- Effective Drying: Rotary dryers excel at efficiently drying potash ore by utilizing indirect heating and hot air to ensure quick and uniform drying, resulting in consistent product quality.
- Versatility: In addition to potash ore drying, rotary dryers find utility in drying various other minerals such as limestone, kaolin, and gypsum, showcasing their versatility in industrial applications.
What is the principle of Rotary Dryer?
- Direct Rotary Dryers: Direct rotary dryers operate by facilitating direct contact between the material and process gas, effectively drying materials. They find extensive use across various industries, such as fertilizer and agriculture, mining and minerals, specialty chemicals, and more, owing to their enhanced efficiency and adaptability.
- Indirect Rotary Dryers: In contrast, in indirect fired dryers utilize heat emitted from the drum’s shell to dry materials through radiation and conduction, circumventing direct contact between the materials and drying air. Indirect rotary dryers are typically favored for small or medium batches where product contamination or degradation risks exist due to exposure to the atmosphere, or when handling toxic and/or hazardous chemicals that should remain isolated from the environment. opt for an indirect rotary dryer when drying highly combustible materials, organics like grain and pulp, and fine substances such as pigments.
Which heating way should I choose: co-current flow or counter-current flow?
- Co-current Air Flow: Rotary dryers offer two airflow configurations: co-current and counter-current. Co-current airflow implies that the material moves in the same direction as the heating medium flow. This setup provides better control over solid material temperature and prevents overheating, although it’s marginally less thermally efficient than counter-current airflow.
- Counter-current Air Flow: Counter-current flow heating involves the material moving opposite to the heating medium’s direction. While more efficient, it offers less temperature control and a higher risk of overheating.
The choice between heating methods depends on the material’s characteristics and the overall process requirements.
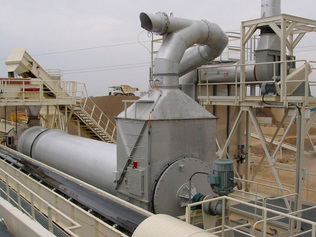
Application of Use
The rotary dryer has a very wide range of applications and can meet the drying requirements of various industrial materials.
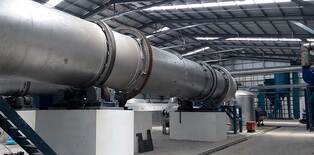
Powder Particles
- Sand
- Silica Sand
- Aggregates
- Limestone
- Clay
- Mineral Filter Cake
- Coal
- Iron Sulphate
- Fly Ash
- Gypsum, Etc
Damp and Sticky Materials
- Coal Slime
- Sewage Sludge
- Bentonite
- Kaolin, Etc
Corrosive Materials
- Distillers
- Grains
- Fertilizers
- Animal Manure
- Slag, Etc
Biomass Materials
- Sawdust
- Wood
- Chips, Etc